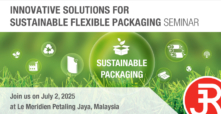
Innovative Solutions For Sustainable Flexible Packaging Seminar
(July 2)
Packaging Material Solutions
Free Seminar
Production processes are becoming progressively more challenging. Besides core processes, the handling, conveying, mixing, and dosing of raw materials need to be optimized and adapted to an increasingly complex manufacturing environment.
The optimized control of material distribution in existing and new factories can reduce failures and operating costs drastically. With smart concepts and perfectly dimensioned components, we provide individual solutions that address these issues and further stabilize the overall process.
Whether you need material handling for a plastification unit on your injection molding machine, an extruder on your cast or blown-film line, or any other plastic converting process, we can offer smart, high-quality solutions to optimize your material flow.
Taking a holistic approach, our first step is to analyze your existing production processes and material flow to identify your individual requirements together with you. Based on this information, and together with our deep process know-how in different applications in the plastics industry, we then develop a smart tailor-made concept up to the required level of automation. Our concept provides flexibility for enhancements should you encounter the need for future adaptations.
Mr. Kristian Rieck
Head of Industry, Packaging Material Solutions
Email: [email protected]
You can bring your production to a whole new level by automating your material handling system to your preferred degree – beginning from single dosing units with an exact scaling up to the complete control and visualization of the whole system, including the integration of the silos. Our smart concepts for small and large scale, high-quality machines, combined with our local technical support will undoubtedly ensure your processes are safe.
A South-East Asian converting company with currently more than 100 injection molding machines and manual material distribution faced the usual difficulties of this kind of process setup, such as faulty material distribution, high level of required manpower and floor space as well as high traffic on site to distribute the individual raw material to the machines.
If nothing is shown here , there is no current event for this industry available.