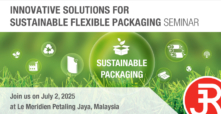
Innovative Solutions For Sustainable Flexible Packaging Seminar
(July 2)
Packaging Material Solutions
Free Seminar
Stable production processes are key for you to stay ahead of the competition and continue being successful. With the perfect chiller solution, you can achieve maximum efficiency for your machines. Additionally, you will benefit from reduced operating costs by saving energy and water, and also support your continuous high production quality level.
A significant part of the energy and water savings is achieved through the optimal choice of chillers and setup of the cooling system with its parameters, saving up to 95% water and up to 60% energy compared to conventional evaporative cooling tower systems.
Whether you need a process cooling system for your injection molding machines, your cast or blown-film lines, or any other plastic converting process, we can offer the right concept to meet your specific requirements. It is a matter of choosing the right dimensioned system to be able to save as much energy as possible, whilst fulfilling the cooling water supply.
To develop the ideal concept for your factory, our first step is to analyze your existing production setup. Based on this information, we then develop a tailor-made solution that will improve your production by enhancing your productivity, reducing your operating costs, and ensuring the safety of your processes. Our concept provides flexibility for enhancements should you encounter the need for future adaptations.
Mr. Kristian Rieck
Head of Industry, Packaging Material Solutions
Email: [email protected]
By implementing the right cooling system, you can take advantage of a stabilized production and reduced operating costs. This can be on any scale you wish – ranging from single temperature control units to air cooled chillers or even complete factory cooling solutions.
As specialists in the field, we can help to further optimize your plastic processing production with our tailor-made process cooling solutions. These are suitable for all plastic processing applications. Our smart and scalable concepts, high-quality machines, and local technical support are your guarantee of safety in production.
An Asian plastic converting company, which specializes in sheet extrusion and thermoform machines producing cups, lids and trays for coffee houses, and ready meals, were using open cooling towers to chill their running machines. This equipment requires an initially low investment, but also entails high operating costs owing to water evaporation, energy consumption and the usage of additional chemicals. As a result, the company was losing out on profits in view of the low throughput and rising energy costs.
If nothing is shown here , there is no current event for this industry available.